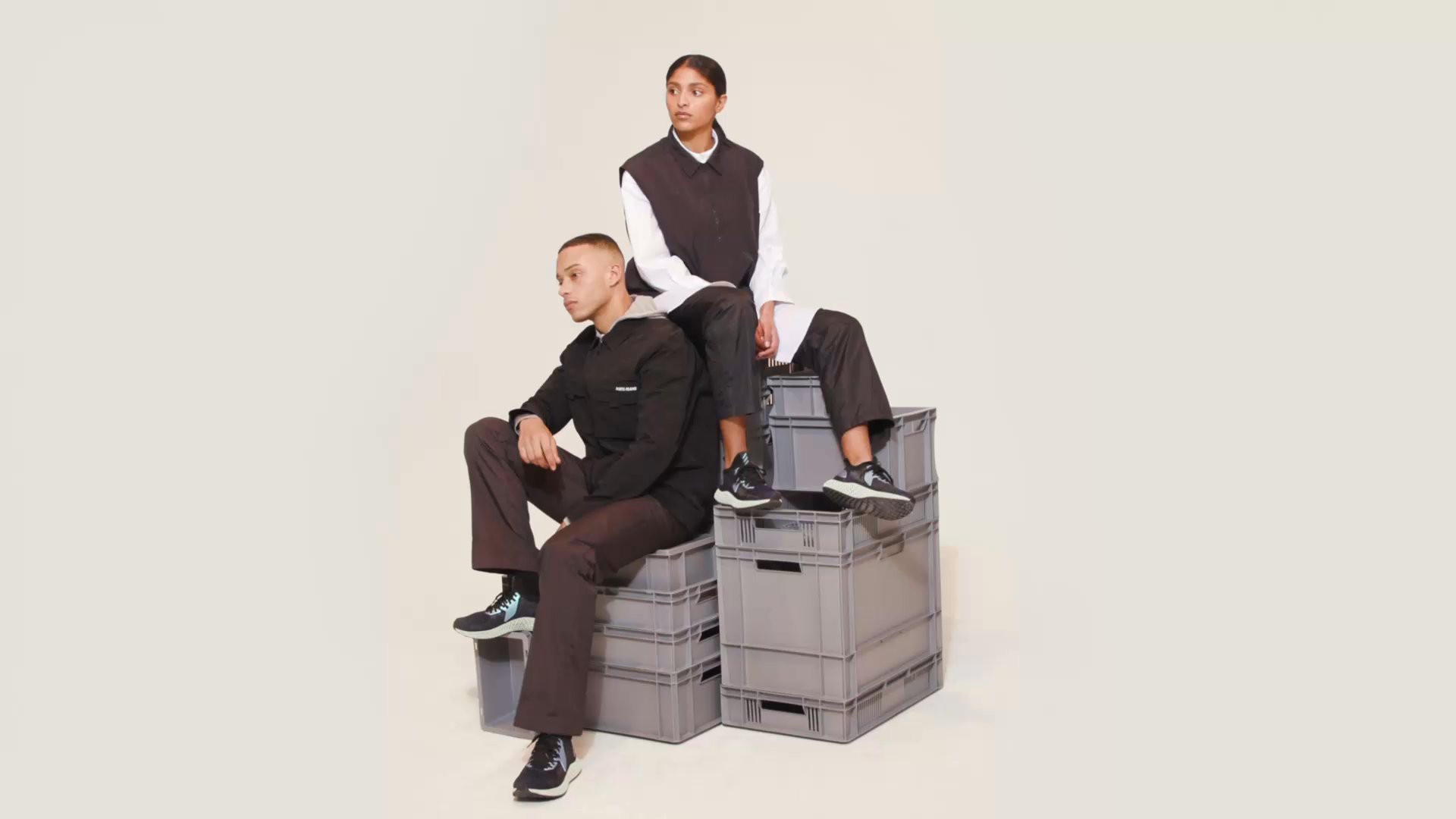
It’s not often that a technology comes along that completely rethinks how a sneaker is made. But in 2013, adidas achieved this with Boost and again, four years later, with adidas 4D technology.
Since its launch in 2017, adidas has scaled production of the 3D printed sole from just a handful of limited-edition sneakers to over 100,000 pairs. The now-signature sole has appeared on models across all of adidas’ categories including Originals' ZX franchise and Y3, as well as on collaborative designs with Daniel Arsham, Hender Scheme, and Disney's Star Wars. As 2019 draws to a close, adidas has released the AlphaEdge 4D, a fitting holiday drop that features a navy upper with galaxy-inspired iridescent panels.
When an adidas 4D sole first appeared on the Futurecraft 4D in April 2017, it had sneakerheads and athletes alike instantly intrigued. The unconventional choice of sole color – a pastel green that adidas termed ‘Aero Green’ – already went against the customary white, black, or gum palette. But what most people were really curious about was the lattice structured midsole. What was it made from? How was it made? How did it feel?
The intrigue came from the fact that there wasn't anything else like it. Unlike uppers, there is little scope for variation when it comes to soles. Materials are generally limited to EVA or rubber, and the process of making a sneaker’s midsole has hardly changed over the years. Molding, either by compression or injection, remains the most widely used method as it is cost-effective for large scale production. This technique doesn’t allow for customization nor quick tweaks in design, and any alterations require a new mold to be created, a task that is both timeconsuming and expensive.
Adidas 4D, however, removes these barriers by using 3D printing. Within its ‘Futurecraft’ innovation lab, adidas had been experimenting with digital printing for several years when it came across Silicon Valley 3D specialists Carbon. Unveiled during a TedTalk in 2015, Carbon invented what is known as Carbon Digital Light Synthesis (DLS) technology, a precise 3D printing technique that gave high-quality results, and did so fast. The two companies joined forces and used DLS to translate years of athlete data into a responsive, cushioned, and commercially scalable 3D-printed midsole. In the future, adidas aims to use this method to create personalized soles that are perfectly tailored to the individual’s specific needs.
Although complete personalization remains the final goal, the technology isn't quite there yet. But, the AlphaEdge 4D which is available to buy now, is more than enough to keep adidas 4D enthusiasts satisfied thanks to its futuristic appearance and supple, springy underfoot feel. Adding to the cutting-edge sole, the AlphaEdge 4D colorway features a super-lightweight upper made of Primeknit – another of adidas’ hallmark innovations –iridescent panels, and a sturdy Continental rubber outsole.
The AlphaEdge 4D is available now at adidas.com/4D and adidas' new LDN Oxford St flagship store.